The proposed project is an inter-disciplinary innovation action aimed at improving the new DLE H2 technology from a current maturity level TRL5 via TRL6 up to the demonstration in a system prototype at TRL7. Emphasis is placed on ensuring operational, mechanical, and thermophysical integrity, an on a framework for safety handling pertaining to H2 gas-turbine operations fueled with mixtures of NG and hydrogen from 0-100% H2.
The specific methods and facilities to achieve the objectives of the HyPowerGT project are described in the following:
Experimental facilities
Baker Hughes gas turbine test bench & Sesta lab
The demonstration of the DLE H2 technology capability at TRL6 will be performed at Sesta Lab, a well-recognized combustion lab, where the NovaLT™16 combustion system has been developed and tested for years. Sesta Lab can replicate the full-scale boundary conditions of the full scale instrumented annular combustor in terms of flows, temperatures, and pressures; concerning fuel flexibility, it is possible to test any blend of natural gas and hydrogen.
The demonstration of the DLE H2 technology at TRL7 will be carried out in a full scale prototype on Baker Hughes test bench in Firenze, where the DLE H2 combustion system will be integrated with a 16.9 MWe NovaLT™16 gas turbine engine. The system prototype will be operated through a wide range of operating conditions, and fuel mixtures of hydrogen and natural gas, up to 100% H2. As shown in the picture below, the engine prototype will be equipped with special instrumentation mainly on the combustion system hardware, which will provide useful data to the validation of the analytical models developed within this project.
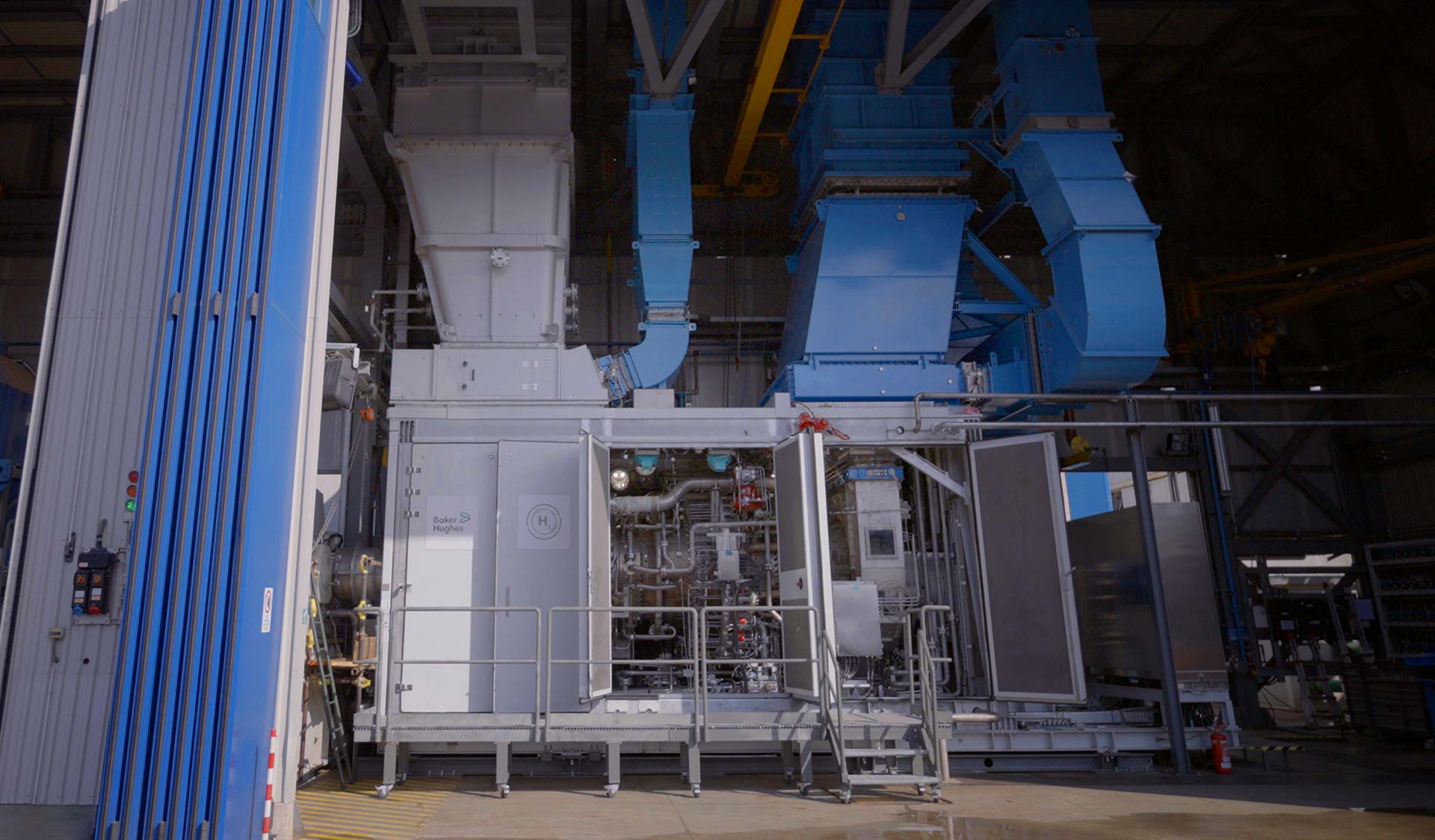
ZHAW combustion lab
The combustion test rig at ZHAW is specifically designed to measure flame dynamics and perform thermoacoustic tests. The test rig consists of an optically accessible combustion chamber equipped with quartz glass windows, water-cooled condenser microphones up- and downstream of the burner, and speakers for both upstream and downstream forcing. This allows for measuring flame transfer matrices (FTM). The flame transfer function can be derived from the FTM or alternatively obtained by combining multi-species chemiluminescence measurements. Additionally, laser diagnostic techniques, such as particle image velocimetry (PIV) and laser-induced florescence (LIF), can be applied to study the flame structure in detail. The lab is designed for thermal powers up to 200kW. Two fuel lines can provide arbitrary mixtures of hydrogen and methane and the fuel storage facility is sized for long duration testing. An electrical air pre-heater can reproduce typical gas turbine combustion chamber inlet temperatures of up to 650 °C. The lab is also equipped with a gas emission measurement system (CO, CO2, NOx, etc.)
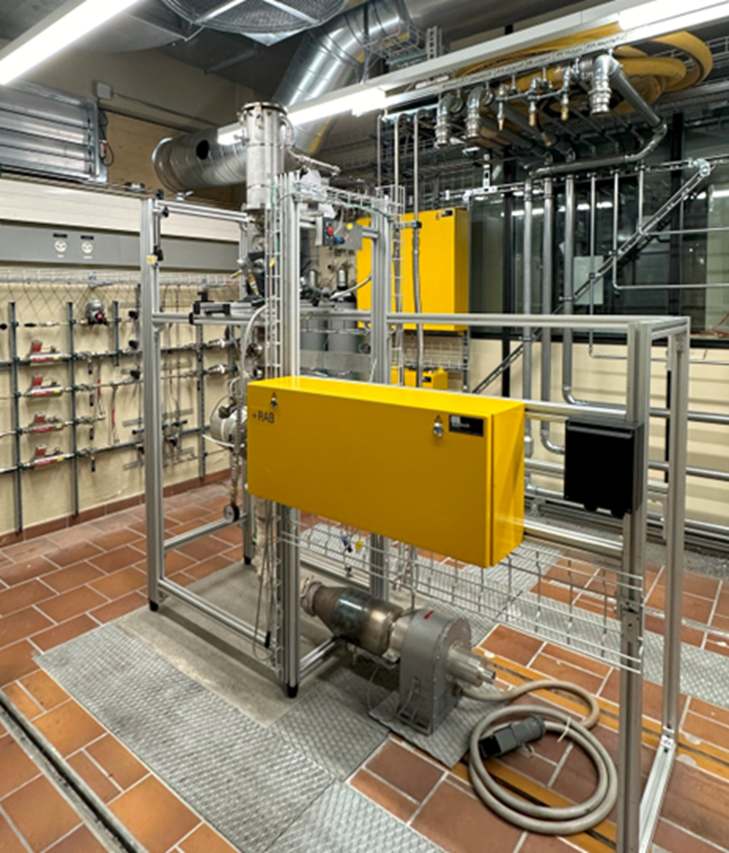
Numerical simulations
To analyse risks in H2-operated gas-turbine engines, CERFACS will perform Large Eddy Simulations of possible ignition sequences of unsteady scenarios using AVBP, a high fidelity solver, recently adapted and tested for hydrogen combustion in an advanced European Research Council grant. AVBP will make it possible to simulate mixing of hydrogen and air in non-nominal scenarios defined in cooperation with project partners.
Further information on the AVBP can be found at this link on CERFACS website.
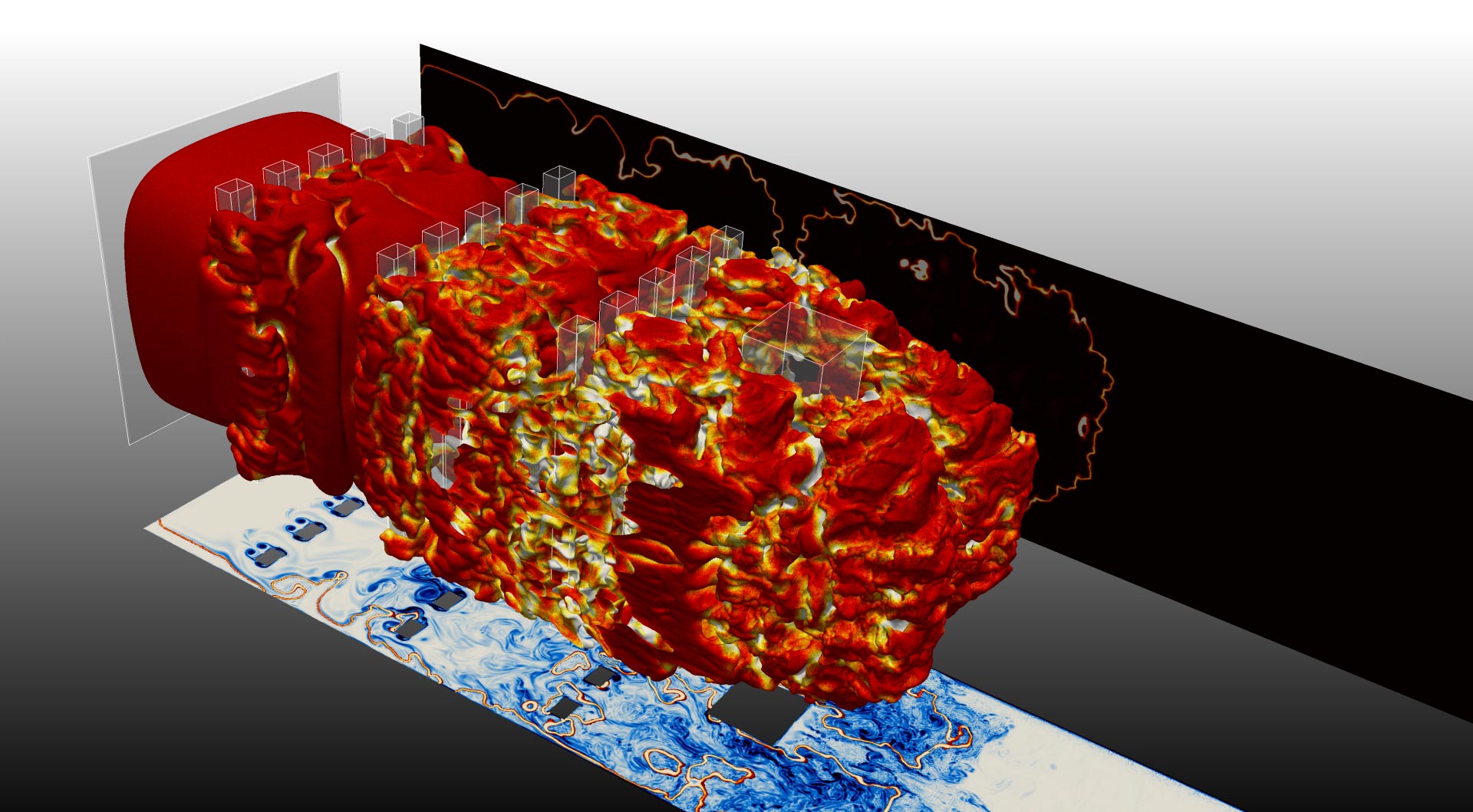
DNS – Code
SINTEF exploits an open-source Direct Numerical Simulations (DNS) tool to obtain accurate estimates of the burning rate (combustion velocity) that characterises turbulent premixed hydrogen-air flames at high pressure. The DNS tool selected to perform this research is part of the Pele Suite of hydrodynamics simulation codes for reacting flows and features Adaptive Mesh Refinement (AMR), a crucial requirement to simulate turbulent combustion processes at high pressures. The planned numerical investigation consists of a series of DNS of canonical, statistically planar turbulent premixed hydrogen-air flames configured at conditions that are representative of those present in the combustion system of the NovaLT™16 gas turbine, ranging from part- to full-load operation.
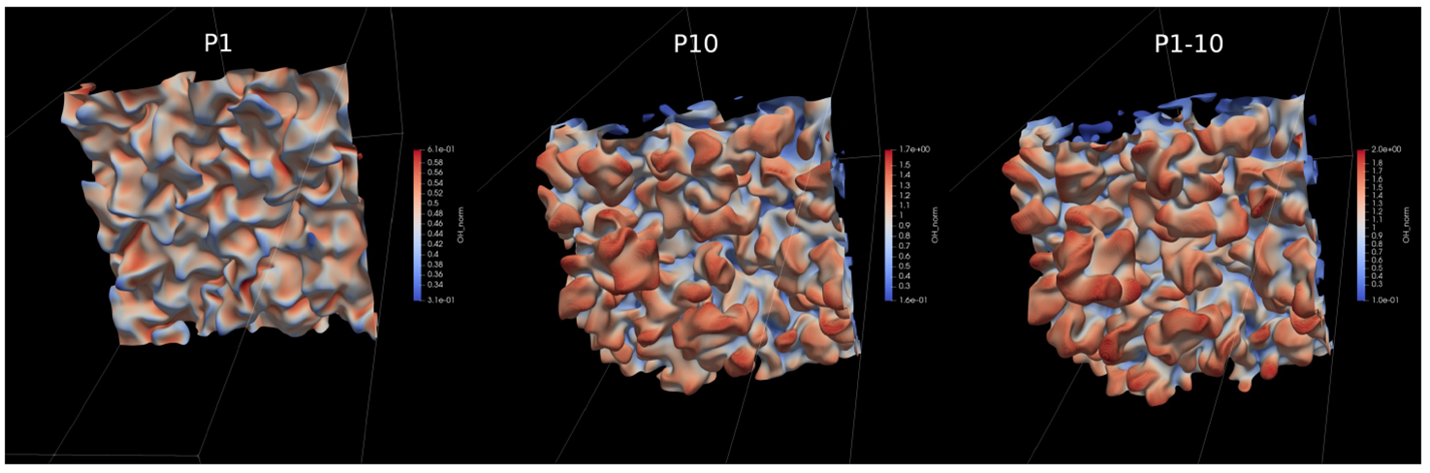
Numerical simulations
Baker Hughes uses 3D detailed LES based modelling for the large part of the analysis required during the design process of combustion systems: relevant examples are the self-excited flame instabilities simulations (see figure) and the flashback risk assessment. Effort will be directed at extending the tools validation to Hydrogen case to assess the combustion-system stability and the exhaust gasses composition of the new DLE H2 technology.
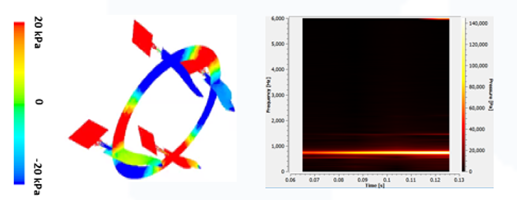
Theory/low order
ZHAW makes use of network models to represent the thermoacoustic behavior of combustion systems. This approach is very powerful in simulating many different operation conditions due to its low computational cost as when compared to high-fidelity numerical simulations. Network models describe the system’s thermoacoustics as a modular network of subsystems into which the system is divided, e.g., plenum, burner, flame, combustion chamber as shown in the figure below.
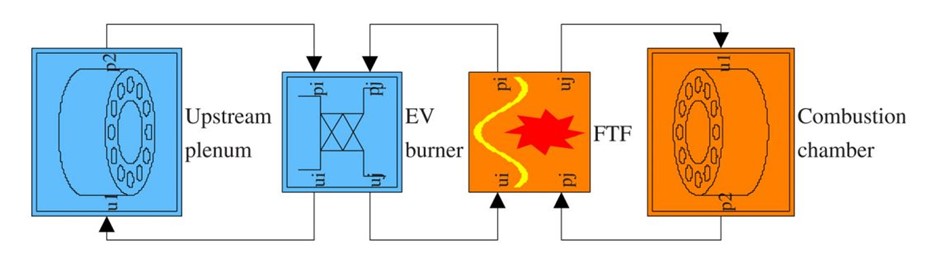
The single subsystems relate upstream and downstream acoustic velocities and pressures and are connected to each other allowing for plane wave propagation between the elements. One of the key advantages of network models is their hybrid approach: numerical, experimental, and analytical techniques are combined to describe the real system.
The acoustic variables for the single network modules, i.e., acoustic pressure p and particle velocity u, are expanded on a modal basis to obtain a state-space representation of the acoustic propagation. By doing so, the acoustic input–output behavior of a subsystem is described. If the geometry of a respective subsystem is sufficiently simple, its acoustics can be described analytically. For complex three-dimensional geometries, finite element calculations (FEM) are used. In this case, the FEM results are converted into state-space models, which can be connected to other network blocks. The acoustic characteristics of the flame are incorporated by means of FTFs/FTMs and source terms, which are obtained by fitting state-space models to measured data.
For the network model approach used in HyPowerGT, FTFs are measured at atmospheric conditions and subsequently scaled to the respective operating pressure. In addition, the network model can be used to identify or optimize suitable countermeasures as for example acoustic dampers and burner staging.
Safety planning
Safety risk management when using substances classified as dangerous is of paramount importance. Hydrogen poses two hazards: it is classified as extremely flammable (Hazard Statement H220) and, as gas, it is stored under pressure (Hazard Statement H280). Hence, HyPowerGT includes, as part of its demonstrations scope, the analysis and assessment of the safety risks that may arise with the retrofitting of existing gas turbines with the hydrogen combustion technology systems.
The safety risk analysis will include:
- Health, Safety and Environment (HSE) assessments;
- Failure Modes, Effect and Criticality Analysis (FMECA) of the physical conversion of the existing gas turbine fuelled with 100% hydrogen;
The analysis and evaluation of safety risks emerging from the application of the hydrogen-retrofitted turbines in real industrial environments will also be logged in a public available safety management plan.
Roadmapping
A roadmap for DLE H2 technology exploitation will be developed within the HyPowerGT project. This involves employing a scenario-based methodology to evaluate the progression of hydrogen-operated gas turbines in the 10-20 MWe class towards commercialization by 2030. Subsequently, it entails navigating through the positioning phase from the early 2030s until the successful conclusion of the European energy transition by 2050.
The roadmap will identify technology and normative gaps and risks associated with maturing DLE H2 technology through TRL8 and subsequent market uptake, outlining necessary R&D for potential market segments. The roadmap evaluates implications across technological, political, regulatory, financial, and commercial aspects, including BH’s product portfolio integration and licensing potential. LUCART, as a CHP plant operator, will engage in the roadmapping together with SNAM, BH and SINTEF.
Regulation, Codes, and Standards (RCS) analysis across EU countries, particularly Italian regulations, will assess technology development and market perspectives, highlighting regulatory burdens and possible bottlenecks. Practical industry and power sector cases, alongside emerging mechanical drive capacities for H2 infrastructure, will be explored.
The approach aims to align project outcomes with EU Green Deal objectives to accelerate industrial sector decarbonization.